1. Failure: Unwinding correction limit
Reason: When the unwinding mechanism is wearing the tape, the tape is not centered in the mode
Solution: Adjust the sensor position or center the reel position
2. The upper and lower limits of the discharge floating roller are faulty
Reason: The discharge pressure roller is not pressed tightly or the winding tension is not opened, and the potentiometer is abnormal
Solution: Press the discharge pressure roller or open the winding tension switch, and recalibrate the potentiometer
3. Failure: travel correction limit
Reason: The travel correction is not centered or the probe is abnormal
Solution: reset the center setting, check the probe position and whether the probe is damaged
4. Failure: winding correction limit
Reason: The belt is not centered in the mode when the rewinding mechanism wears the belt
Solution: Adjust the sensor position or center the reel position
5. Failure: the back roller has no opening and closing action
Reason: The back roller has not completed the origin calibration or the calibration sensor state is abnormal
Solution: re-calibrate the origin or check the origin sensor status and signal whether it is abnormal
6. Failure: Back roller servo failure
Reason: abnormal communication or loose wiring
Solution: Press the reset button to reset the fault or power on again, check the alarm code query manual
7. Failure: the second side is not intermittently coated
Cause: Fiber failure
Solution: Check whether the coating parameters or the optical fiber signal are abnormal
8. Failure:Doctor Blade servo failure
Reason: The servo driver for tool adjustment alarms or the state of the sensor is abnormal, and the equipment stops in an emergency.
Solution: Check the emergency stop button or press the reset button to eliminate the alarm, recalibrate the origin of the scraper roller and check whether the sensor status is abnormal
9. Malfunction: Scratches
Reason: caused by slurry particles or the scraper is chipped
Solution: feeler gauge to clear particles, check scraper
10. Failure: powder drop
Reasons: a. Over-baking causes powder loss; b. High humidity in the workshop and water absorption of pole pieces; c. Poor adhesiveness of the slurry; d. The slurry has not been stirred for a long time.
Solution: Contact Field Quality Technology
11. Failure: Insufficient areal density
Reasons: a. Large drop in liquid level; b. Walking speed c. Knife edge
Solution: Check the speed and knife edge parameters, and keep a certain liquid level.
12. Failure: more particles
Reasons: a. The slurry itself is carried or precipitated; b. The roller is caused by the single-sided coating; c. The slurry is not stirred for a long time (static state)
Solution: wipe off the roller before coating, if the slurry has not been used for a long time, you need to consult the quality technology whether it is stirred or not
13. Malfunction: Smearing
Reasons: tailing of slurry, gap between back roll or coating roll is not parallel, back roll bounce speed
Solution: adjust the parameters of the inter-coating gap and increase the speed of the back roller
14. Failure: Positive Dislocation
Reason: The alignment parameters are not corrected when there is an alignment error
Solution: Check whether the foil materials is slipping, clean the back roller, press the reference roller and press the roller, and correct the alignment parameters
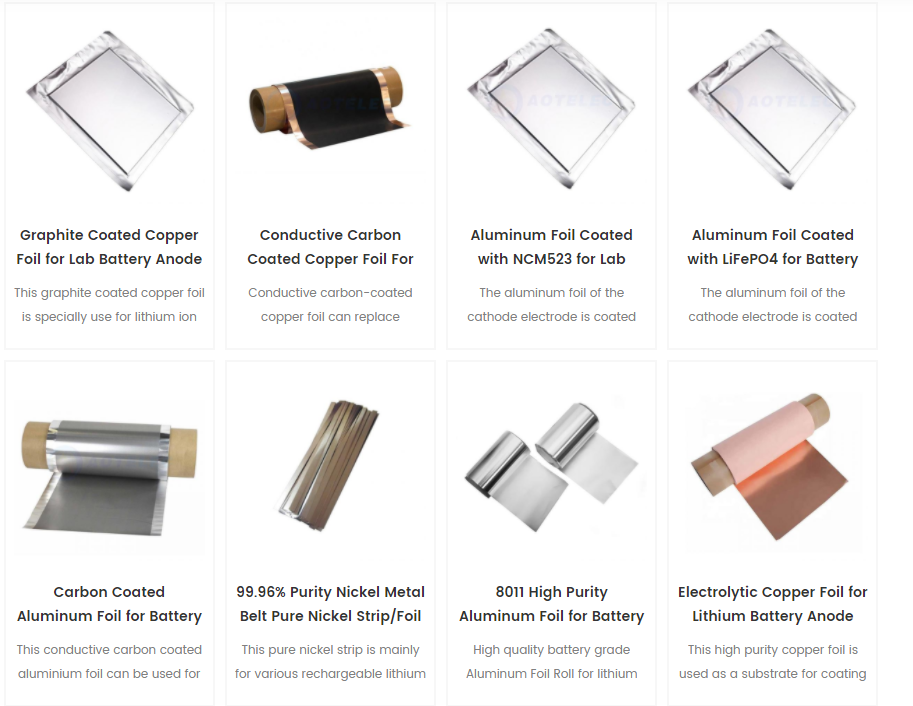
15. Failure: The coating on the reverse side is parallel and trailing
Reason: The distance between the back coating rollers is too small, too small or the back roller bounce distance is too small
Solution: adjust the spacing of the backing rollers and increase the bounce distance of the backing rollers
16. Failure: the head is thick and the tail is thin
Reason: The thinning parameters of the head and tail are not adjusted properly
Solution: Adjust the head-to-tail speed ratio and the head-to-tail starting point distance
17. Failure: coating length, intermittent process change
Reason: There is slurry on the surface of the back roller, the traction rubber roller is not pressed, and the gap between the back roller and the coating roller is too small and too tight
Solution: clean the surface of the back roller, adjust the parameters of the intercoating, press on the traction, rubber roller
18. Failure: There are obvious cracks on the pole piece
Reason: drying speed is too fast, oven temperature is too high, baking time is too long
Solution: Check whether the relevant coating parameters meet the process requirements